Smart manufacturing is the information driven, event driven, efficient and collaborative orchestration of business, physical and digital processes within plants, factories and across the entire value chain.
Smart Manufacturing Technologies and Skill Sets
The Texas Defense Aerospace Manufacturing Community (TDAMC) targets the following smart manufacturing technologies and skill sets:
- 5G wireless networks (industrial Internet of Things)
- Smart sensors
- Edge computing
- Cloud data/computing
- Digital twins
- Artificial intelligence
- Machine learning
- Cybersecurity
- Advanced human-machine interfaces
- Virtual reality/augmented reality
- Additive manufacturing (for rapid prototyping and production)
Benefits to Manufacturers
The benefits of smart manufacturing to manufacturers include:
Cost/profitability – Automation reduces cycle time, labor time and quality errors. Continuously monitored resources and artificial intelligence-driven insights alert on unusual patterns and suggest improvements.
Asset reliability – Asset performance monitoring leads to higher levels of use, and predictive insights lead to higher reliability.
Quality – Monitor quality aspects of products in real-time to reduce process variability, eliminate undetected errors and catch issues as early as possible.
Energy productivity – Energy costs are directly saved as processes are optimized based on energy usage insights. They are indirectly saved as the waste of resources is decreased by reducing defects, scraps and overproduction of inventory.
Why Smart Manufacturing?
Successful implementation of smart manufacturing technologies, workforce training, and assistance to small and medium-sized manufacturers through our program can strengthen Texas to be the dominant ecosystem and location for defense aerospace manufacturing in the U.S. It can also continue to widen the gap between Texas and other locations.
Smart manufacturing is becoming the model of modern manufacturing. It includes most of the U.S. Department of Defense modernization priorities (Section 8, Fiscal Year 2020 Industrial Capabilities Report to Congress).
Smart manufacturing is considered a “must-have” for future manufacturing competitiveness. Experts generally agree that successful smart manufacturing enterprises will leverage the expanded use of automation and create a convergence of interconnected information technology (IT) and operational technology (OT) into an increasingly digital workflow.
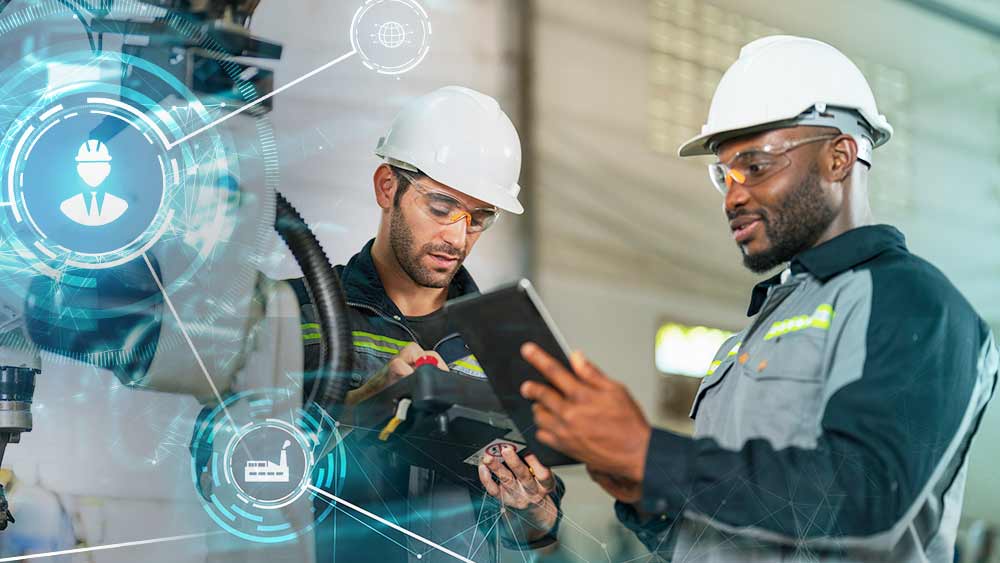
This integration with upstream and downstream stakeholders at every level of the supply chain with detailed product and process history (digital twin) ensures the quality, security and integrity of manufactured components.
Though aerospace manufacturers were early leaders in using digital manufacturing, they lag behind many industries in adopting the cyber-physical interface throughout the manufacturing workflow.
Some of this is attributable to cultural and practical resistance within the industry. But much of it can be traced to disconnects between the workforce skills and general technology familiarity needed to incorporate smart manufacturing methods into the production supply chain.
Smart Manufacturing Value Proposition
The smart manufacturing value proposition for defense aerospace production is the same as for all industries. If properly implemented, it offers greater manufacturing flexibility with reduced costs and better quality.
Smart manufacturing tools and their associated cost savings will inevitably become contract requirements to serve the government customer. Early adoption of these technologies positions manufacturers with potential competitive advantages in the near term. These tools will also help contractors meet customer needs by supporting product lifecycle data development with design, production, inspection, fielding, repair and disposition.
Smart manufacturing aspires to combine manufacturing, data and management into an integrated, agile and highly efficient system.
Five key attributes characterize smart manufacturing systems: connected, optimized, transparent, proactive and agile. These attributes are achieved by designing and implementing flexible manufacturing systems where equipment, personnel and data are coordinated in a digital framework.
In addition to affecting choices of manufacturing processes, this involves expanded use of automation and sensing, bridging data between IT and OT systems. It also includes applying advanced analytics, such as artificial intelligence and machine learning, to support better decision-making.